We highlight important aspects of the COSHH system of controls and give examples of measures for hazards that Cura Terrae provide consultation for.
Measures to control exposure to hazardous substances are a major part of the UK’s occupational health and safety legislation. In this article, we focus on controls. We highlight important aspects, give examples of controls for key hazardous substances, and explain why involving a consultant like Cura Terrae can be invaluable in safeguarding your workforce.
A part of COSHH
The implementation of control measures to reduce exposure to substances that can cause disease constitutes one of the Control of Substances Hazardous to Health (COSHH) Regulations.
In full, the COSHH regulations protect workers and necessitate that, if hazardous substances are used in a workplace, the risks must be suitably assessed and addressed.
What are “substances hazardous to health”?
Hazardous substances subject to COSHH regulations include:
- chemicals
- products containing chemicals
- fumes
- dusts
- vapours
- mists
- nanotechnology
- gases and asphyxiating gases
- biological organisms
They may be procured and used directly, generated during working activities, or occur naturally, such as grain dust.
Commonly, hazardous substances have a Workplace Exposure Limit (WEL), decided by the UK Health and Safety Executive (UK HSE). However, if a substance doesn’t have a WEL, it’s not necessarily safe. It may be that there is not yet sufficient data to define a WEL; the substance is not inhaled (WELs refer to concentrations in air); or a safe level of exposure does not exist.
Once hazardous substances have been identified, the risks should be assessed. This involves understanding who is exposed, the route (e.g., inhalation, ingestion, or skin contact) and level of exposure.
Exposures highlighted by the COSHH Risk Assessment should then be prevented. Ideally, this would mean eliminating the substance completely. For example, by changing the process or activity so that it is no longer needed or generated, or by using a safer alternative.
Only if exposure cannot be prevented should control measures be considered.
Types of control measures
Control measures consist of both equipment and changes to ways of working. A combination of the two is vital. Simple practices can make huge differences, and no equipment, however practical, will be effective unless used properly.
Control measures have a hierarchy
The UK HSE’s guide to COSHH places control measures in order of priority. If the prevention efforts described above are not feasible, the following control measures can be considered, in order of decreasing preference:
- Use a safer form of the product, e.g., a paste or pellets instead of a dusty powder.
- Change the process to emit less of the substance, e.g., reduce the temperature so that less vapour is released.
- Substitute a hazardous substance with one that is less hazardous, e.g. replace organic vapours for degreasing metals with an aqueous-based cleaner such as citric acid.
- Enclose the process so that the product does not escape.
- Extract emissions of the substance near the source.
- Have as few workers in harm’s way as possible.
- Provide personal protective equipment (PPE) such as gloves, coveralls and a respirator.
Staying in control: check and maintain
The correct use, functioning, and maintenance of controls are also regulated under the COSHH framework. This means ensuring that control equipment is working in the way that it is meant to, and that workers are following the correct procedures. Someone should be nominated to oversee this.
Controls should be operational all day, every day.
The value of a consultant
The UK HSE state that it is imperative whoever designs, installs, maintains, and tests control measures is competent, with the necessary skills, knowledge, and experience.
Cura Terrae’s experts have British Occupational Hygiene Society (BOHS) accreditation. We’re also ISO 45001 (Occupational Health and Safety Management Systems) certified. With a wealth of expertise and a proven track record, our team of professionals can support you with:
- Completing your COSHH Risk Assessment.
- Selecting controls for your workplace.
- Workplace Air Monitoring to confirm that your controls are effective.
- Workplace Air Monitoring to ensure WELs are not exceeded.
- Testing of Local Exhaust Ventilation (LEV) controls (see below) to ensure correct functioning.
- Tailored Health and Safety Awareness Training for your workforce, including on the use of controls.
Examples of controls
Here, we look at some examples of controls for hazards that Cura Terrae regularly provide consultation for. However, bear in mind that there are many more options for controls than this, and that many of the examples below could be used for different hazardous substances.
Solvent vapours
It is incredibly easy to inhale vapours from solvents, which are used in many workplaces. We discussed the adverse health effects of solvent vapours and the importance of solvent vapour safety here. Risks could be controlled by:
-
Different types of spray equipment
- When applying glues, paints, and paint strippers (such as in the construction industry) conventional spray equipment can generate a lot of overspray and mist, leading to very high levels of solvent exposure. Alternative spray equipment, such as high-volume low-pressure (HVLP) spray guns can reduce this, and is consistent with point 2 above, process changes to emit less of a dangerous substance.
-
Segregation
- When performing work with solvents, measures should be taken to restrict access to the work area for all non-essential personnel. For example, by cordoning it off. If working outside, it is also important to consider wind speed and direction as this can cause spray and vapours to drift large distances.
Formaldehyde
Formaldehyde is a dangerous chemical, but it has many applications. In our Formaldehyde: myths vs facts article, we argued that, despite regulations, it cannot be guaranteed that workplaces using formaldehyde are safe. Safety can be improved by:
-
Use of a glove box
- A glove box is a sealed container. Components inside are manipulated by placing your hands in gloves attached to the box. The process and the user are totally isolated from one another, and so there is little risk of exposure. Indeed, a glove box represents point 4 above, enclose the process. However, while useful and often employed in laboratories, a glove box or non-automated closed system is not practical for large industrial processes. Local exhaust ventilation (LEV) (see below) may be more effective in these cases.
-
Exposure time reduction
- Planning tasks efficiently to reduce handling time is an example of a “way of working” control. This could form part of a Standard Operating Procedure (SOP). In addition, as a supervisory control, staff can be rotated to avoid prolonged exposure of individuals.
Diesel engine exhaust emissions
In our article on diesel engine exhaust emissions, we explained how they constitute a Group 1 carcinogen, affect many of the body’s systems, and were responsible for nearly 15,000 deaths between 2000 and 2016. Two possible controls are:
-
Local exhaust ventilation
- Local exhaust ventilation (LEV) is characterised by the capture of airborne contaminants as near to the point of their generation as possible. It typifies point 5 above: extract emissions near the source. There are many different LEV systems. The image below shows an example of one for a diesel-powered vehicle. General (mechanical) ventilation is also an option, and is often practical for large workspaces. This is the continuous introduction of fresh air into the working area to mix with and dilute fumes, lowering inhaled concentrations. In the railway sector, ventilation fans in station roofs, linked to timers or sensors at the platform level, can reduce worker and the public’s exposure to emissions from diesel trains.
-
Idling policy
- The establishment of an idling time policy can reduce unnecessary emissions. For optimum impact, the details should align with workplace practices and routines. For example, anti-idling initiatives in the railway sector need to consider crew schedules and breaks, as well as servicing regimes.
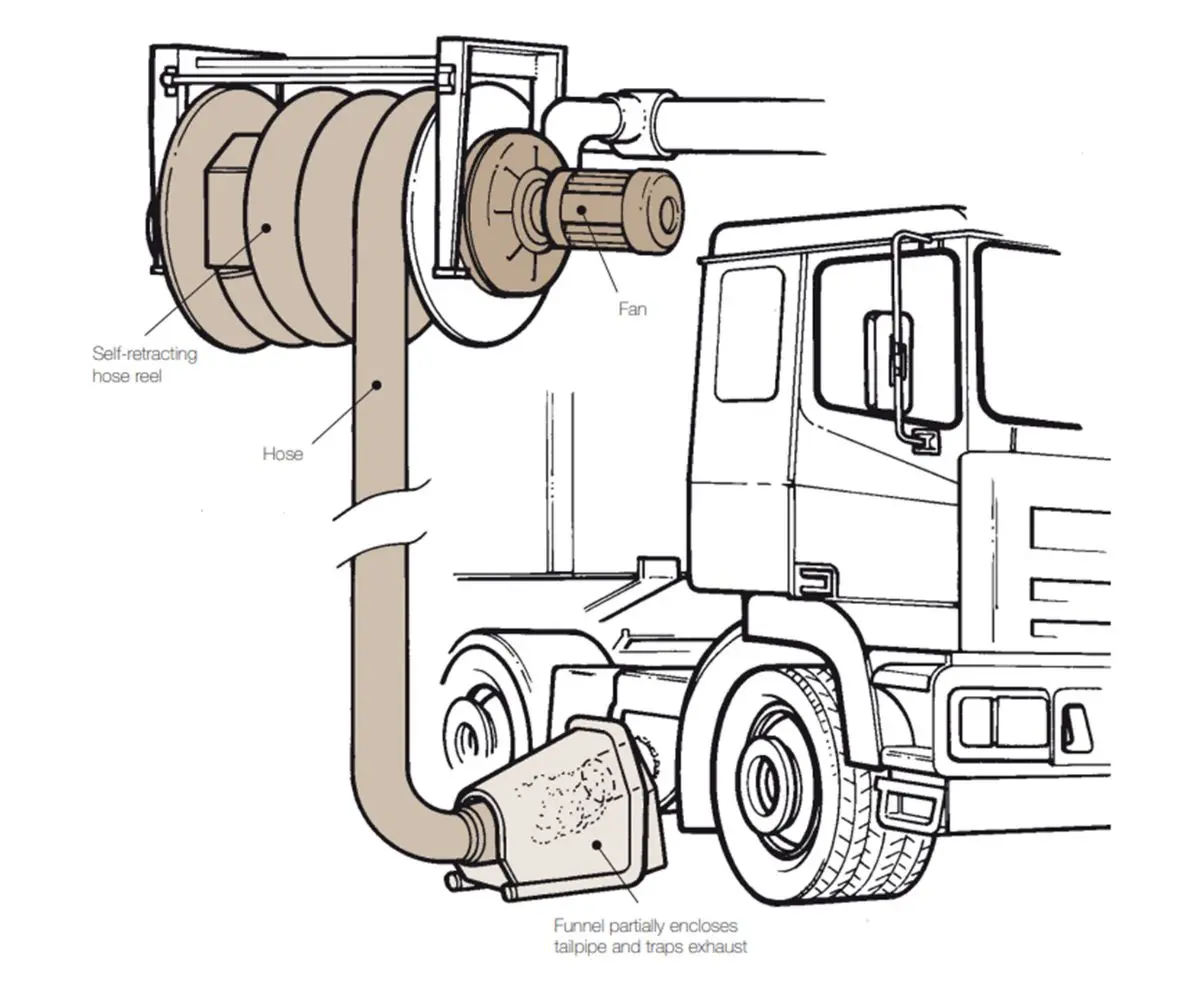
Image source: UK Health and Safety Executive publications.
Metal fume
Dangerous fumes are often generated when working with metals. We investigated their respiratory, cardiovascular, neurological, and cancer risks in our article on managing metal fumes. The following are options for controls:
-
Respiratory protective equipment
- Personal protective equipment (PPE) should always be provided for metal workers such as welders, as well as eye shields for those working in their vicinity. Respiratory protective equipment (RPE) is to be used if adequate control cannot be achieved from LEV alone, or if activities are taking place outdoors. It is commonly classed as a last resort. The right mask or respirator depends on the process being undertaken and the duration of the work, but must be properly fitted. How can you tell if LEV is not adequate in controlling metal fumes? If you’re welding with LEV but not all the fume is captured, clouds of fume may be visible in the air. However, for some types of welding, like tungsten inert gas welding (TIG), fume is not often visible, so you could use a dust lamp or may be able to smell the gases. Soot and residue might also accumulate on nearby surfaces. Our Workplace Air Monitoring can provide empirical confirmation of insufficiently controlled metal fume.
-
Remove grease and all surface coatings
- Before beginning welding, ensure that the metal is fully cleaned and prepared, with all grease and surface coatings removed, as these may contribute to the release of toxic components.
Controls will be specific to your workplace
The ideal controls for you will depend on your site, activities, and workforce. Rarely will one measure be sufficient, and they must all work together. However, taking the time to understand and implement appropriate controls will create a safer and more productive workplace, could optimise processes and cut wastes, ultimately leading to healthy profits.